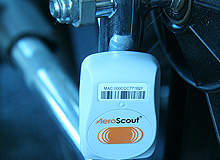
Great Ormond Street Hospital (GOSH) is the UK’s premier paediatric hospital, treating around 25,000 in-patients per year. A couple of years ago the WiFi system in the hospital, used primarily at the time for Electronic Prescribing (EP) and VOIP telephony, was suffering from overload and instability leading to frequent outages. When drawing up the specification for a new WiFi system ICT Director Mark Large and his colleagues took the opportunity to implement a Radio Frequency ID (RFID) system.
The system they selected is based on Cisco medical-grade network that eliminates any ‘single point of failure’ and includes twin wireless controllers. Since installation monthly performance figures indicate 99.9997% availability of the whole network, which equates to 6 minutes per year when something wasn’t working, but with duplication of all key systems none of the users noticed anything was amiss.
RFID tracking of hospital equipment
Most people are aware of RFID used in shops to set off an alarm if someone takes an item out through the door without having the tag removed. These ‘passive’ systems are cheap and simple, they have a coil in the tag which picks up sufficient energy from a coil in the doorway security arch to power a simple transmitter.
Something similar could be deployed in a hospital, with a security arch on each door informing the asset management system each time a device passed through a doorway. But that would only let you know which room or corridor something was in, an ‘active’ RFID system can be much more precise. And by using the WiFi and LAN infrastructure it avoids the need for dedicated security archways and extra wiring all over the building.
To ensure sufficiently accurate location finding WiFi coverage has to be excellent. In old buildings with obscure corners, multiple extensions, extensive modifications and winding corridors that becomes a challenge. In a new building access points are often installed in a grid pattern, each about 9m-10m from its neighbours. At GOSH system installers Block Solutions spent a great deal of time analysing the buildings and wireless signal strength and have installed sufficient WiFi access points to enable any tagged piece of equipment to be located with an accuracy of 2m by triangulating its position from three access points. According to Mark Large this is the best wireless tracking network in the UK.
Of course this high density of access points means that EP, VOIP, data, image and video transfer around the site is fast and reliable.
How well do you really know your competitors?
Access the most comprehensive Company Profiles on the market, powered by GlobalData. Save hours of research. Gain competitive edge.
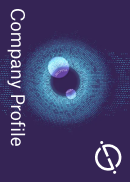
Thank you!
Your download email will arrive shortly
Not ready to buy yet? Download a free sample
We are confident about the unique quality of our Company Profiles. However, we want you to make the most beneficial decision for your business, so we offer a free sample that you can download by submitting the below form
By GlobalDataThe tags and asset management software were supplied by California-based AeroScout Inc. who specialise in WiFi based asset tracking systems for healthcare as well as manufacturing and logistics.
GOSH use a range of different tags with greater or lesser degrees of ‘intelligence’. The most basic are only suitable for location tracking; more sophisticated tags have buttons that users can press to send a message. Precisely what happens when the button is pressed is determined by simple programs loaded into each device by the IT team. The T2 tag is also available with a wrist strap to enable patients to be located in large hospitals, and to give them a readily available ‘panic button’.
Tags are fitted by the biomedical engineering team using a variety of means, but cable ties and adhesives are the norm. Any fixing has to be approved by the infection control team. At present GOSH are not using tags on items that have to be sterilised, though AeroScout do make one and it is under consideration for the future.
To reduce network traffic, and prolong battery life AeroScout tags use a ‘beaconing’ method send tiny packets of data on pre-defined intervals. They also have motion sensors to put them into sleep mode when not moving, saving yet more power. The batteries give up to four years service, give a warning when low and can be replaced by users.
Data from the tags is aggregated by AeroScout’s Mobile View software, enabling staff to find things quickly and managers to control the hospital’s assets.
Stuart Stagg, Head of Bio-medical Engineering at GOSH gave us a simple example of how RFID can save time. A couple of months before we spoke to the portering team, responsible for moving patients around the hospital, had acquired 12 new wheelchairs which were all tagged before being pout into service. After two months the manager of the portering service compared the hours the wheelchairs were in use and the time spent by porters looking for them and retrieving them with the time wasted on un-tagged wheelchairs, and concluded that in two months they had saved 36 man hours.
What to tag, and when?
The question of what to tag, and when, is important. Causing disruption by taking items out of service for tagging isn’t ideal so in general items are tagged when newly bought or when returned to Bio-medical Engineering for servicing. Some specialist items thought to be particularly significant were tagged as a matter of urgency. GOSH currently has some 1,700 items tagged, but AeroScout have customers tracking tens of thousands.
One of the first items to be tagged at GOSH during the initial testing phase was a light source used with fibrescopes in opthalmology. This is primarily used in day clinics, but was often borrowed out of hours for use elsewhere, on wards or in training. On several occasions this lead to routine clinics being delayed while the light source was located.
The mere presence of a tag on a device has a ‘motivational’ effect on staff who are less likely to forget to return an item if they know it can be traced; since tagging the light source it has gone missing only once, and Stuart was able to provide a report of where the device had been in the last 24 hours leading to its rapid recovery.
The Health and Social Care Act 2008 relating to the prevention and control of infections imposes new regulations on hospital mattresses as from April 2010, at GOSH every mattress was replaced, and fitted with programmable tags. Now, any time damage to the mattress cover is spotted a simple press of the button on the tag sends an email to the infection control team warning them that this mattress needs attention. The accuracy of the system has also made it a great deal easier to find individual mattresses when they are due a routine check.
Is GPS the future of medical device tracking?
GOSH are still consolidating their RFID system, gradually adding to the number of items tagged. Smaller tags and autoclavable tags will widen the application, and it’s possible they may consider tags with GPS in future for devices taken off site.