
Across the UK there are over 50 hospitals confirmed to be home to a dangerous form of concrete with a stable shelf-life of only approximately 30 years sparking concern and efforts across the country to identify and remove the troublesome material.
Since 2021 the UK government has begun a series of publicly funded initiatives to clean up the previously prolific Reinforced Aerated Autoclaved Concrete (RAAC) after it was found to be prolific across several schools across the UK. A 2021 investigation confirmed that as many as 54 hospitals and medical facilities across the UK were built using the faulty material.
Previously, the discovery of RAAC in use across multiple UK healthcare facilities prompted the creation of draft evacuation plans across a number of affected wards. No hospital was entirely affected, with RAAC being found as part of extensions to previously constructed hospitals, built cheaply by local authorities in the 1950s and 80s. The estimated lifespan of RAAC, before moisture and weather forces cause it to begin to deteriorate, is approximately 30 years. Some structures containing RAAC can be as old as fifty years old.
Responding to the findings of its own investigation, the UK government launched an additional funding initiative of £698 million from 2021 to 2025 for trusts to put in place necessary remediation and failsafe measures.
However, one issue many hospital trusts are facing is that there is no one set of guidance for how the various hospitals and trusts should go about removing the problematic concrete or even identifying and categorising where in a hospital the concrete can be found.
Using the allocated money, some National Health Service (NHS) trusts have attempted different methodologies for identifying and prioritising the removal or mitigation of RAAC, but one hospital trust in Yorkshire has developed a novel system that allows them to accurately map and create floor plans of a working hospital, identifying where across the hospital the offending planks can be found.
How well do you really know your competitors?
Access the most comprehensive Company Profiles on the market, powered by GlobalData. Save hours of research. Gain competitive edge.
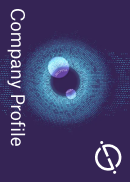
Thank you!
Your download email will arrive shortly
Not ready to buy yet? Download a free sample
We are confident about the unique quality of our Company Profiles. However, we want you to make the most beneficial decision for your business, so we offer a free sample that you can download by submitting the below form
By GlobalDataUsing GIS (Geographic Information System) software from UK-based developer, Esri UK, the system replaces paper-based processes with digital workflows to improve the accuracy and efficiency of RAAC inspections.
The method involved a team of eight inspecting 20,000 RAAC planks across 52 departments. Esri says that the system reveals where the highest risk areas are in real-time, which informs the mitigation works, including temporary propping, steel reinforcements and fixing roof leaks, to maintain the safe operation of the hospital.
Hospital Management sat down with Airedale Hospital’s Estate project manager, Richard Burgin as well as Nick Campbell-Voegt of the consultancy firm, BIS Consult, a partner of Esri UK who developed and implemented the system throughout the hospital.
Joshua Silverwood: Can you give me a little bit of background on how we got to this point?
Richard Burgin: Airedale Hospital was built back in the late 1960s and it was a system built out of RAAC, which is essentially a lightweight non-aggregate cement-like slurry with reinforcement inside of it. It has a design life of thirty years, and we are in excess of fifty now. Back in 2019, there was a safety alert which triggered an NHS estates alert that required all NHS estate facilities to have to go and monitor their respective trusts for this concrete.
As a former charted surveyor, I had the unenviable task of doing that and discovered that approximately 83% of our entire estate was made of RAAC. So that has grown over time from us conducting our initial survey. Originally, we were working using paper and found that there are approximately 20,000 RAAC planks underloading the floor as well as in the roof and then an additional 30,000 in the internal and external walls. So, we had to keep carrying out more and more inspections on each and every one of these planks at different frequencies.
We had to develop a hierarchy of inspection among some of the planks with some of them being inspected more frequently than others. So, we estimate we do approximately 80,000 panel inspections a year.
That’s an awful lot of data to handle. We were writing this all down on pieces of paper, taking photographs and taking them back to the office, producing Excel spreadsheets, creating CAD drawings then putting together all those paper-based packs and then triggering another set of inspections. That was just a system that was becoming more and more unwieldy.
This fantastic tool though, has revolutionized how we inspect and how we manage the data from those inspections.
JS: Can you give me a bit of an idea as to how this mapping system was developed?
Nicholas Campbell-Voegt: The hospital already had a very established and involved process and as Richard explained, they were trying to manage a lot of data and were encountering challenges based on the sheer volume of inspections they had to do. We looked to re-engineer that process so that we could utilise a digital way of working and move away from paper-based surveys and Excel spreadsheets.
Once we had all the information eventually in one place, we created an electronic version of the survey that they were using with questions aligned to Airedale’s system of working and RAAC management guidance. There were several questions that would determine what kind of damage what RAAC panel has and then align that to a certain risk rating that would then indicate how frequently those panels need to be checked.
We basically pulled that all together to create a system that gives them an end-to-end way of managing that data in a more robust way.
JS: Is this methodology unique to Airedale?
RB: Yes, in as much as there is not any other real guidance for hospitals as to how RAAC should be surveyed. We were given a set of risk factors based on defect type and risk factors in the plank which we have funneled into a hierarchy.
Whilst there isn’t a hard and fast approach to surveying, we believe that the approach we have adopted as well as the system that BIS has built to support us, embodies best practice in terms of managing RAAC risk as much as is reasonably possible alongside other structural engineering works.
We’re very proud of what we’ve achieved that we’ve had that independently verified and we have allowed risk assessments to be done by a company called Risk Tech and they’ve highlighted that it meets best practice. You can appreciate such a high level of risk mitigation in terms of the failure of material in a building that sort of got 98% occupancy, 365 days of the year, 24 hours a day.
JS: Can this be rolled out to other hospitals?
NCV: I would see the potential to roll this out to other hospitals and NHS trusts, Airedale and I are having discussions around how it might look to do that in the future alongside our technology partners at Esri. We have had a few discussions with other trusts lined up.
RB: I think that is one of the big benefits we see in this system. If you look at the NHS, it is comprised of what are essentially 240 separate business units. This problem is not just affecting us in the NHS but the wider public sector and the private sector. Considering the problem we have, with RAAC making up approximately 83% of our estate, we have been very fortunate to have the time and resources to develop this learned experience over the last five years. We see the ability in this platform to accelerate others through the system and supporting documentation to help others manage the risk of RAAC as quickly as they can.
So we are looking at ways to offer that out as a platform.”
Whilst there is no one stated system of guidance, the UK government has confirmed that since its initial findings in 2021 as many as four hospitals have entirely eliminated RAAC from their facilities. It also confirmed that seven hospitals that are most affected by RAAC are also part of its New Hospital Programme, headed for full replacement by the end of 2030. Systems like those produced at Airedale Hospital are symptomatic of a problem that arises with no guidance.